Home > Ultrasonic welding technology
Ultrasonic welding technology
WHAT IS
Ultrasonic technology is a sophisticated welding method that allows joining two different plastic parts into a single object without the use of chemical reagents or glues.
Ultrasonic welding works at a molecular level with thermoplastic polymers. A small percentage of these plastics is necessary for ultrasonic technology to work.
The direct consequence of ultrasonic soldering technology lies in its application in a wide range of fields.
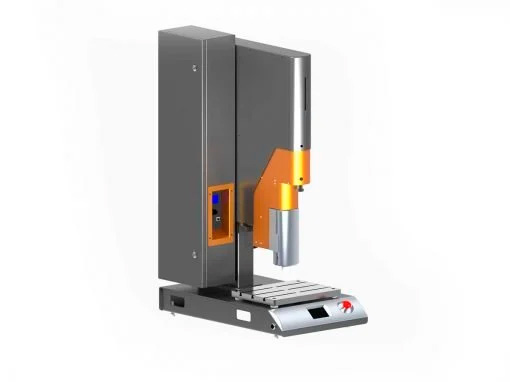
HOW DO ULTRASOUNDS WORK
In order to get two items welded correctly, some essential elements are required: first and foremost high-frequency and low-amplitude vibrations, these generate heat melts plastic components on its interface.
These frequencies, undetectable for the human hear, are called ultrasonics.
Placement of parts during the welding process can be either manual or automatic, depending of the application. One of them gets fixed in a static holder while the other part gets exposed to sinusoidal ultrasonic vibration that is perpendicular to the contact area, emitted by a ultrasonic sonotrode.
Friction obtained from these ultrasonic vibrations causes heat, thus remixing the plastic polymers of both parts. Once cooled down, said polymers stabilize and create a weld.
New systems regulated by computers have been devise to adjust welding times and amplitude and above all the amount of delivered energy on the two parts’ contact area and guarantee an optimal welding.
Components and operation mode
Ultrasonic equipment usually comprises a generator, a converter, a booster and a sonotrode.
Ultrasonic generators are capable of reaching electrical frequencies up to 20 kHz.
These electrical frequencies are transformed into mechanical movement by a converter that contains piezoelectric ceramics.
Such mechanical movement is transferred to the booster afterwards, increasing its amplitude until reaching the sonotrode.
Then the sonotrode transfers the vibration into the two items subjected to the welding process.
Operation mode
The vibration amplification chain is the most important part of the system, designed taking into account various vibrational phenomenon that develop within it. It begins from converter – or piezoelectric transducer – that transforms electrical power into mechanical power, or rather vibration. This is a very complex system, built to operate to the chosen frequency of work.
Booster and horn are fixed to transducer through screws; this latter is the sonotrode (literally “what leads sound”). These devices amplifying the wave generated by the piezoelectric converter and are manufactured in order to maintain the same frequency to the whole system.
Booster amplify the amplitude of vibration. Sonotrode, built with the final part flattened, has the same function, to concentrate vibration on the final part, in strength contact with material to be welded.
Ultrasonic equipment noise
Just like every machine tool, depending on their application, even ultrasonic equipment can be a source of ambient noise. All ultrasonic products made by Sonic Italia have been conceived to operate beyond threshold of human hearing (1700-1800 Hz). Equipment’s oscillations fall within a range of 20, 30 40000 Hz and are not perceptible The extensive incursion of thermoplastics in major technological fields such as automotive, white goods, electrical parts, medical and military gear, has permitted to create a wide range of applications.
It is necessary to prepare and apply different measures of protection when using blare-generating machines.
- Earmuffs (individual protection, local noise)
- Welding tool guards against localized sonance
- Soundproofed cabins for collective protection and block high level of noise
Components built and marketed by Sonic Italia do not generate any kind of radiation. Any potential sound nuisance that might be caused by machinery is due to a mechano-acoustical effect of air resonances that generates sound waves. As in concordance with Italian Law (L. 89/392 att. 1 step 1.5 parag. F). In any case, according to the statistics, only 15-20% of our applications cause high-level noises. Sonic Italia offers its technical expertise for consultancies for soundproofing studies with the assistance of its network of suppliers and qualified technicians.
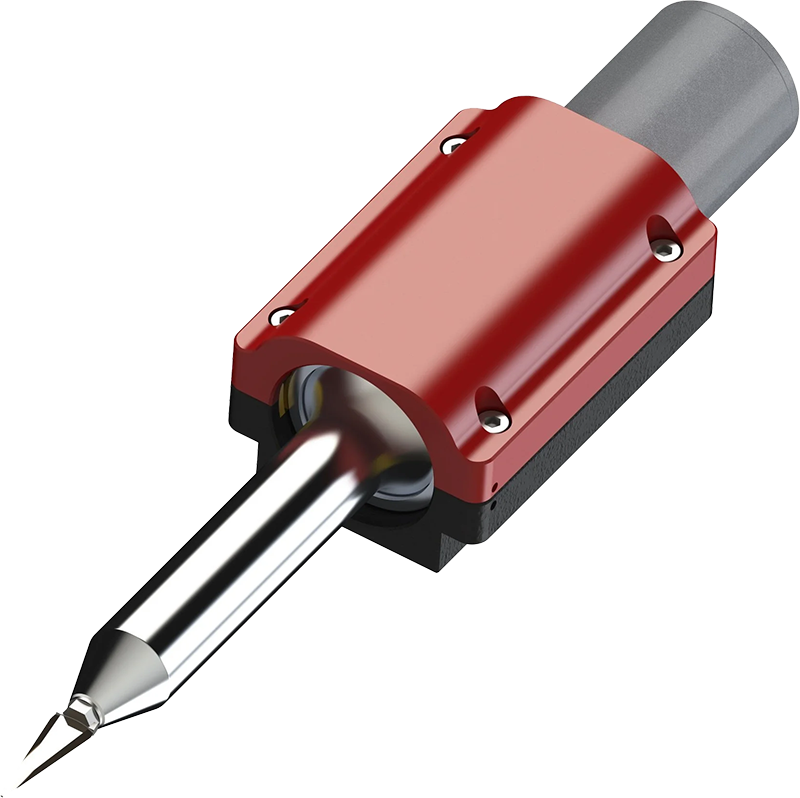
Materials and weldability
Riveting and welding are two different ways to assemble industrial components.
Riveting consists in merging a mass of materials and shaping it like the head of a rivet with the purpose of combining two different elements such as plastics and metal.
The benefit of this method is that the sonotrode can be traced back once the materials are cold, keeping the pieces rigidly anchored.
Ultrasonic welding with energy directors on the other hand, it is necessary to consider many factors: the type of raw materials, shape, injection or thermoforming deformations during molding, the soldering variety (mechanical, liquid-tight, pressure-sensitive), sonotrode distance into the surface area, etc.
To have some constructive recommendations and technical data about ultrasonic technology, you can get several useful documents at the download section. Sonic Italia technical staff will gladly find a solution that suits your business needs.